I have followed the techniques described below in
making my trees. Lynn Gobin was a member of the now-disbanded West
Side Lumber Co. Model Railroad Club of Rochester, MN. Their web
site is still on line. Click their logo to visit it. The
article below is copied from their site because I do not know how much
longer their site will remain active. Many thanks to Lynn Gobin for giving me permission to
publish his article here. You can visit Lynn's current model
railroad work at his personal web site, the Zumbro
Valley and Western.
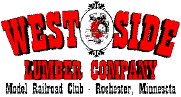

I have added a few comments
on my experience with Lynn's techniques at the end
of this page

Tree Construction
Lynn Gobin
Materials
A tree trunk armature Use anything that looks like a miniature
tree of the scale, height, and species you want to model. I prefer sage
brush twigs for larger deciduous trees like mature oaks and cottonwoods.
For birches and smaller deciduous trees, I use pieces from a decorative
broom I bought at a Ben Franklin craft store. You can, of course, use
anything that looks like a tree, from yarrow and goldenrod weeds; to
herb and tree roots; to manufactured cast metal and plastic armatures.
Ground
foam Ground foam represents the leaves of the tree. You can
certainly use Woodland Scenics ground foam, but I prefer AMSI. (Your
favorite hobby store can order AMSI ground foam from Walthers.) I think
AMSI ground foam is lighter and fluffier than Woodland Scenics. And, in
my opinion, AMSI ground foam colors are more muted and more realistic
than Woodland Scenics. For any tree, mix different colors and textures
of ground foam. Remember, not all the leaves on a tree (or the sides of
an individual leaf) are all exactly the same size and color. I’ve
included a chart of the colors and texture mixes I use.
Woodland Scenics Polyfiber Used to build up the volume of the
tree’s foliage.
Here's an interesting and cost-saving tip from Paul R.
Rivers, Webmaster of the NMRA:
You can use plain old white poly pillow stuffing to make trees if you
paint it black beforehand. The application of black paint also adds an
illusion of depth to the tree.
Fast drying clear spray enamel or lacquer Stiffens the
Polyfiber foliage, readying it to accept the ground foam leaves.
Hair spray This is the world’s cheapest spray adhesive, and
is used to glue the ground foam to the Polyfiber. I suppose you could
use some other brand, but I prefer Aqua Net Unscented Super Extra Hold
in the pretty lavender can. (Can anyone explain why an “unscented”
hair spray includes fragrance in its list of ingredients?)
Another fine tip from Paul R. Rivers: The
cheaper the hairspray the better. The cheapest brands are usually
diluted clear varnish in a spray can.
Ground Foam Color and Texture Mixtures
The following table of foam color and texture mixtures is used
courtesy of Sweetwater Scenery Products. For realistic scale model
scenery and supplies, contact Sweetwater Scenery Products, PO Box 4242,
Casper, WY 82604, (307) 237-8474.
Species |
Parts |
AMSI Ground foam color/texture |
AMSI
catalog
number |
Oak |
1
1
1/4 |
Olive Medium
Grass Green Medium
Olive Fine |
432
442
431 |
Silver Maple |
1
1/4
1/16 |
Grass Green Medium
Grass Green Fine
Spruce Fine |
442
441
551 |
Elm |
1
1/4 |
Medium Tree Texture
Grass Green Fine |
207
441 |
Ash |
1
1/4
1/8 |
Grass Green Medium
Grass Green Fine
Yellow Green Fine |
442
441
411 |
Cottonwood |
1
1/2
1/4 |
Olive Medium
Eucalyptus Medium
Olive Fine |
432
562
431 |
Sycamore |
1
1/2
1/4 |
Gray Green Medium
Olive Medium
Olive Fine |
472
432
431 |
Poplar |
1
1 |
Spruce Fine
Grass Green Fine |
551
441 |
Aspen |
3
1
1 |
Grass Green Fine
Spruce Fine
Timber Products Meadow Green Course, #102-12 |
441
551
- |
Birch |
1
1
1/2 |
Medium Tree Texture
Grass Green Fine
Olive Fine |
207
441
431 |
Assembly Instructions
- Prepare the tree trunk armature by trimming it to size. Optionally
(but preferably for larger trunks), "peg" the bottom of
the trunk with a small wooden dowel or a nail so you have something
to stick and glue your tree into your layout.
- Prepare your ground foam mixture, and put a cupful in a shaker
container with 1/4" holes.
- With your fingers, tease out a golfball-sized chunk of Polyfiber
into a thin sheet.
- Cut out a postage stamp-sized (or smaller) piece of the Polyfiber
sheet. With two tweezers, tease out this piece of Polyfiber until it
is as thin, as wispy, and as lacy as you can possibly make it.
- Using the tweezers, pull the Polyfiber piece onto an individual
branch of the tree. If you are using an armature of a natural
material like sage brush, you won’t need to glue the Polyfiber to
the armature. Natural materials have enough surface texture to grab
and hold the Polyfiber in place. Manufactured armatures, however,
like those made from cast metal or plastic, might be too slippery,
and sometimes need just a touch of some sort of adhesive to hold the
Polyfiber.
- Repeat steps 4 and 5 until all of your branches are covered with
the Polyfiber. Remember that when you look up through the branches
of a real tree you see mostly blue sky. So on your model tree, leave
plenty of empty space, and maybe a "dead" branch or two.
- Fast path alternative: Instead of cutting, teasing, and
pulling small pieces of Polyfiber onto your tree armature, take the
sheet of Polyfiber from step 3 and drape it over the entire tree.
Tease the Polyfiber around the branches.
Please use a spray booth or an
appropriately rated mask or respirator during this step! (I use
both.) Spray the Polyfiber foliage base with clear enamel or
lacquer. Set aside and let dry for at least 15 minutes. This will
ensure that the Polyfiber sticks to the armature. The enamel or
lacquer also stiffens the Polyfiber, thus preparing the fiber to
receive the ground foam.
- Liberally spray the Polyfiber foliage base with hair spray,
avoiding, if possible, those parts of the trunk and branches you
don’t want covered with ground foam. Immediately go to the next
step!
- Turn your tree upside down and sprinkle the ground foam mixture
onto the still-wet-with-hair-spray Polyfiber. Cover the bottom side
of the foliage base on each branch. Then, turn your tree right-side
up and finish sprinkling the foam mixture onto the tree. Stop
sprinkling the ground foam just as the Polyfiber starts to
"disappear."
- Suggestion: Sprinkle the ground foam over a grocery bag or
some newspaper. The "over sprinkle" can be reused on other
trees.
- Tap off the extra ground foam and lightly spray with hair spray.
Let dry for at least 15 minutes.
- Using your scissors, trim off any stray Polyfiber strands.
- Lightly spray one last time with hair spray.
- Plant, and stand back and marvel at your creation!
Tips
 | Use a darker green ground foam on the underside of the foliage and
a light sprinkling of yellow or yellow-green on the top of the
foliage. These add shadow and highlight to the foliage and provide a
greater sense of depth.
 | I can’t stress enough how important it is to tease out the
Polyfiber as much as you possibly can. Your goal should be to build
a tree that you can see through.
 | Vary the color and texture of your ground foam mixtures, certainly
from species to species, but also from tree to tree.
 | Expect to spend a lot of time with each tree. Although relatively
simple to do, this technique can require up to an hour per tree.
Putting the Polyfiber on the armature is time consuming and,
frankly, boring. But sprinkling on the ground foam is quick, fun,
and rewarding! That’s when your tree really takes on life!
 | If you’re making a bunch of trees all at once, try building them
all one step at a time. For example, prepare all the trunks, then
fiber all the armatures, and so on.
 | And one last reminder: please use a spray booth or a respirator
when using spray enamel or lacquer! |
| | | | |

John Hubbard's Comments
I have built two sets of trees. I had some white
polyfibre when I built the first set, and used some Hunter Green spray
paint to color it. The polyfibre for the the second set came from
the Woodland Scenics Moonshine Still kit and was already black. The
black polyfibre definitely gives a better appearance, because it seems to
disappear as the "leaves" are added and does not give such a
dense green appearance. Also, I found that a gentle touch with
the application of the leaves is important. Too many leaves gives a
fuzz ball appearance, whereas a lighter covering, where the black
polyfibre just begins to fade into the background, is more authentic
looking (at least to my eye).
This page last updated 01/15/2007
|